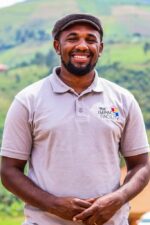
Cyrus Njonde Maina
Other posts by Cyrus
- Into the Field: Learning, Leading, and Growing with The Impact Facility
- Unlocking Kenya’s Mining Potential: Reflections from the 2024 Annual Mining Investment Conference and Expo
- The Impact Facility’s Experience On The Roll-Out of the Mine Investment Partnership Plans (IPPs)
- Formalisation and Financial Inclusion Dialogue of Artisanal and Small-scale Gold Mining in Kenya
- Empowering Women in Gold Processing Through Financial Literacy Training