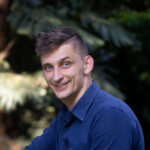
David Sturmes
Other posts by David
- Case Study on The Impact Facility’s Kenyan Equipment Lease-to-Purchase Investment Model In Artisanal and Small-Scale Gold Miners
- Britishvolt joins the Fair Cobalt Alliance to help develop responsible, fair and transparent cobalt supply in the DRC
- How to respond in moments of crisis
- The London Metal Exchange partnered with The Impact Facility to launch a school improvement project in the Copper-Cobalt belt of the DR Congo
- The Fair Cobalt Alliance welcomes its latest members CMOC and IXM